YKK® SNAD® Fastener Adhesive-Backed Flexible Base Stud White 40mm
SKU: 104453




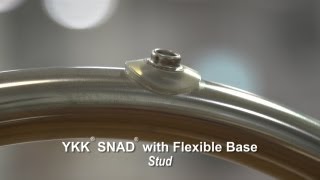
YKK® SNAD® Fastener Adhesive-Backed Flexible Base Stud White 40mm
SKU: 104453
Price per Pack
SNAD studs are alternatives to traditional screw studs for cloth-to-surface uses. They attach to solid surfaces with adhesive – no drilling needed.
Description
SNAD® studs are an alternative to traditional screw studs for cloth-to-surface applications. They attach to a solid surface with adhesive and can be used wherever a conventional screw stud might be used. You can also use SNADs to replace existing screw studs without filling the holes.
Opaque silicone SNADs adhere to hard surfaces with 3M™ VHB™ conformable acrylic foam tape (located on the underside). For more than 20 years, the VHB product line has proven to be tough in marine, automotive, medical, aerospace and architectural applications.
SNADs can be applied to glass, metal, fiberglass, varnished or painted wood, and other hard surfaces. This 40mm fastener has a stainless steel snap stud and a flexible silicone body.
Why Use SNADs?
SNAD Fasteners allow you to attach cloth-to-surface applications to wood, fiberglass, metal and more without drilling into the hard surface.
SNADs are especially important for use with fiberglass boats. It can be difficult to drill a clean hole in fiberglass without cracking or chipping the gelcoat top layer. Damage to gelcoat is expensive and time-consuming to repair correctly.
It’s much faster and less expensive to use SNADs. The SNAD adhesive will not damage the hard surface, and you can simply replace a worn SNAD when the adhesive fails after prolonged use. You never have to risk damage (and the repair costs that come with it) by drilling into a hard surface when you use SNADs.
SNAD Selection
Sailrite® carries 25mm and 40mm SNAD studs with plastic or silicone bases. When shopping for your project needs, it’s important to consider both a SNAD’s size and its base material, as these properties affect holding power and longevity.
- Size: 25mm. This smaller SNAD option has less surface area for its adhesive, contributing to a grip with lower longevity. However, this small size is easy to hide behind your projects, making it less noticeable in a finished application.
- Size: 40mm. A larger size means greater surface area for the adhesive, and therefore a stronger grip over time. However, this larger SNAD is more challenging to conceal, and it may be visible in a finished project.
- Base: Plastic. Plastic SNADs have better dimensional stability and tensile strength. They will not flex when pulled on and can be used heavily, just like mechanically installed screw snaps. Since they cannot bend, they are suitable for smooth, flat surfaces only.
- Base: Silicone. Silicone SNADs conform to curved or uneven surfaces for convenient snap placement anywhere. However, they flex when unsnapped, lifting the adhesive away from the hard surface and reducing its strength and longevity. Silicone SNADs are perfect for “set and forget”-style projects that will not be snapped or unsnapped frequently.
Please Note: SNADs are intended to be consumable items. Their adhesive may fail after a prolonged period of normal use. Additionally, they are not meant for load-bearing applications or for areas with high shear pressure; expect higher failure rates for SNADs used under improper conditions. SNADs are not covered by a warranty and will need to be repurchased to replace those that fail due to improper use or normal wear and tear.
To prolong any SNAD’s adhesion, Sailrite recommends pressing on the SNAD base with one hand while pulling the snap apart with the other hand. This will help the SNAD last longer by reducing stress on the adhesive. Simply ripping an installed item free from the SNAD will eventually cause the part or the adhesion to fail.
Surface Preparation & Application Guidelines
- Clean the surface with a 50/50 isopropyl alcohol (rubbing alcohol) and water mixture.
- Let air-dry or wipe dry with a soft, lint-free cloth.
- For best results, prime the surface with 3M™ Tape Primer 94 Adhesive Promoter (#120671 or #104166).
- Remove the liner from the back of the disk.
- Position the snap and roll into place.
- Press down on the snap, working all the way around and in the center to secure it to the surface.
Application Pressure: Bond strength depends on the amount of adhesive-to-surface contact developed. Firm application pressure develops better adhesive contact, improving bond strength.
Application Temperature: Ideal application temperature range is 70ºF to 100ºF (21ºC to 38ºC).
Dwell Time: After application, the bond strength increases and reaches its strongest point after 72 hours at 70ºF (21ºC). Typical bond strength buildup:
- 20 minutes equals 50% bond strength.
- One hour equals 75% bond strength.
- One day equals 90% bond strength.
- Three days equals 100% bond strength.
Specifications
Brand | YKK |
---|---|
Certifications | Berry Amendment Compliant |
Color | White |
Hardware Material | RubberSiliconeStainless Steel Grade 304 |
Size | Line 24, 0.600" |
Dimensions
Front | |
---|---|
A. | 1.576 inches |
B. | .400 inches |
C. | .316 inches |